The
shale shakers are mainly powered by the rotation motors to rotate and produce
the periodic changed passivity force, drilling fluid that contain solid phase
pass through the mesh screen, do the forcing movement on the mesh surface, and
then the solid phase debris with various size will be filtered. The separation
sizes and through put of the
shale shakers is the most important factors of making use decision. The technology
level of shale shakers mainly show at the treating capacity, the stability of filter
debris,
the life of operation and the flexibility of operation. The managing ability of shale shakers
is related with the structure of shale shaker steel
body, the
movement arrangement, the vibration frequency, the vibration intensity, the working area of shale shakers and
the degree of thickness. In order to make the shale shakers match with the
drilling machineries, the maximum outputs of the drilling pumps and
the quantity of drilling cuttings filtered must be considered.
Shale shaker is one of the main
products of GN solids control .GN sell a
series of solids control equipment and drilling waste management equipment
including vertical cuttings dryer , shale shaker , screw conveyor , shear pump , oilfield shale
shaker , mud cleaner , desander
and desilter , vacuum degasser , poor boy degasser
, decanter centrifuge , mud tank , mud agitator , etc
.
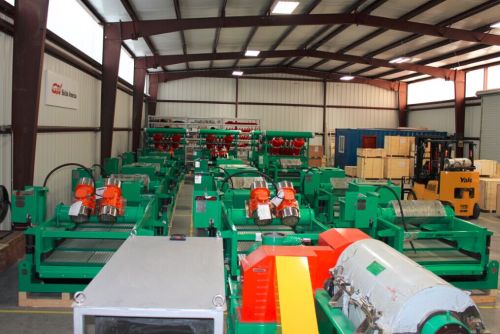
The classification of shale shaker
It depends on the movement arrangement; the shale shakers can be
grouped into round screen shaker, the common elliptic screen shaker, linear
screen shaker, equilibrium elliptic screen shaker. The common elliptic screen
shaker: also can be called the disequilibrium elliptic screen shaker, there is
a exciter devices fixed right above of the screen box , the screen boxes may tilt an angle, use the
leverage of the gravity, avoids the sand having the tendency of back flowing. From this, the tilt of
the screen boxes really improved the flowing performance of sand, but
the disposed amount of the drilling fluid reduced, this is the main disadvantage of the common elliptic
screen shaker. The linear shale shakers: Two main axises with eccentric blocks
do synchronous reverse rotation to produce the liner vibration. Because the
direction of the liner shale shaker is unchanged, which makes the debris difficult to fall
through,
and then the screen paste aspect appears, which makes the
valid over flowing area of screen and throughput reduced. When the number of screens
increases, the aspect of screen paste will be more serious. So when the linear
shale shakers use the super fines screen, it could not meet
the requirements of the using amount of drilling fluid.